Metal Stamping Processes: From Prototyping to Automation
Metal Stamping Processes: From Prototyping to Automation
Blog Article
Exploring the Globe of Metal Stamping: From Design to Manufacturing
Within the realm of manufacturing, steel stamping sticks out as an accurate and reliable technique for shaping metal sheets right into numerous forms with impressive uniformity. From the first layout phase where complex patterns take form to the elaborate manufacturing procedures, steel marking is a blend of creativity and design. Exploring this globe unveils a complex interplay of creativity and technological mastery, using a glimpse into a realm where innovation fulfills workmanship.
History of Metal Stamping
Steel stamping, a commonly used manufacturing process today, has a rich background that dates back to old times (Metal Stamping). The origins of metal stamping can be traced to old human beings such as the Egyptians, who utilized stamping methods to adorn precious jewelry and accessories with intricate designs. With time, metal marking advanced, with worlds like the Greeks and Romans utilizing it for producing coins and attractive products
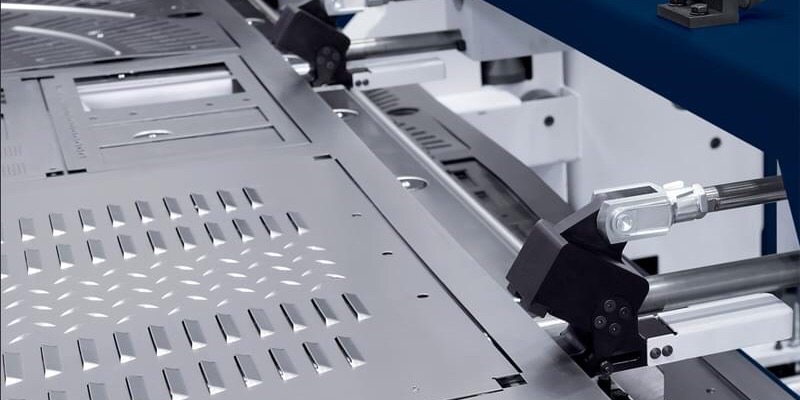
In the 20th century, metal marking remained to evolve with the assimilation of automation and computer numerical control (CNC) modern technology. These developments better increased the effectiveness and accuracy of metal marking processes, making it a crucial part of modern-day manufacturing across markets such as automotive, aerospace, and electronic devices. Today, metal stamping continues to be a crucial manufacturing procedure, combining custom with advancement to satisfy the demands of a regularly evolving market.
Layout Factors To Consider and Prototyping
When developing steel marking projects, meticulous focus to design factors to consider and prototyping is important for ensuring optimum manufacturing outcomes. Style considerations in metal stamping include material choice, component geometry, tooling style, and manufacturing usefulness. Choosing the right material is critical as it affects the part's efficiency, expense, and manufacturability. Component geometry affects the intricacy of the stamping procedure and the functionality of the last item. Tooling design plays a significant function in the success of metal stamping projects, impacting part accuracy, device durability, and manufacturing effectiveness.
Prototyping is a vital stage in the metal stamping procedure that enables designers to check the layout, validate manufacturability, and make needed adjustments before full-blown production. By thoroughly taking into consideration design aspects and utilizing prototyping, suppliers can simplify the steel marking process and achieve high-grade, affordable manufacturing results.
Tooling and Devices Essentials
Considering the crucial function that tooling design plays in the success of metal marking tasks, understanding the vital tools and tools required is critical for achieving efficient manufacturing results. Fixtures hold the steel in area during the marking process, ensuring precision and repeatability. Spending in high-quality tooling and devices not just enhances manufacturing performance but likewise leads to higher precision, minimized waste, and total price financial savings in steel stamping operations.
Production Refine and Quality Assurance
Successfully handling the manufacturing process and applying robust quality assurance actions are crucial for making sure the success of steel marking jobs. The production process in steel marking includes a series of actions that should be very carefully worked with to attain optimum outcomes. It begins with the moved here prep work of raw products, followed by the arrangement of the marking devices and tooling. Operators then feed the products into the press, where the stamping operation occurs. Throughout this procedure, it is important to check the assembly line for any problems that might influence the top quality of the stamped components.
Quality assurance in metal marking is paramount to deliver items content that satisfy the required specifications. Inspecting the stamped components at different stages of manufacturing aids identify any type of issues at an early stage, protecting against pricey rework or scrap. Strategies such as dimensional examination, visual examination, and material screening are generally used to guarantee the quality of the stamped components. By maintaining rigorous quality assurance criteria, makers can copyright their online reputation for delivering top quality steel stamped products.
Applications and Industry Insights
In the realm of metal stamping, the successful application of manufacturing processes and top quality control actions directly influences the efficiency and integrity of different industry applications and offers useful insights right into the industry's functional characteristics. Additionally, steel stamping promotes the manufacturing of numerous family home appliances, consisting of refrigerators, washing makers, and stoves, by giving economical remedies for manufacturing long lasting and intricate parts. Recognizing the applications and sector understandings of steel marking is important for enhancing manufacturing procedures and boosting product top quality throughout different Recommended Site markets.

Conclusion
Design considerations, prototyping, tooling, devices, production procedures, and top quality control are necessary elements of metal stamping. With its extensive applications and industry understandings, metal stamping proceeds to be a functional and efficient production process.
Report this page